Exploring the Significant Costs of Sacrificing Quality: Understanding the Consequences
- Donaven Leong
- Sep 14, 2023
- 7 min read
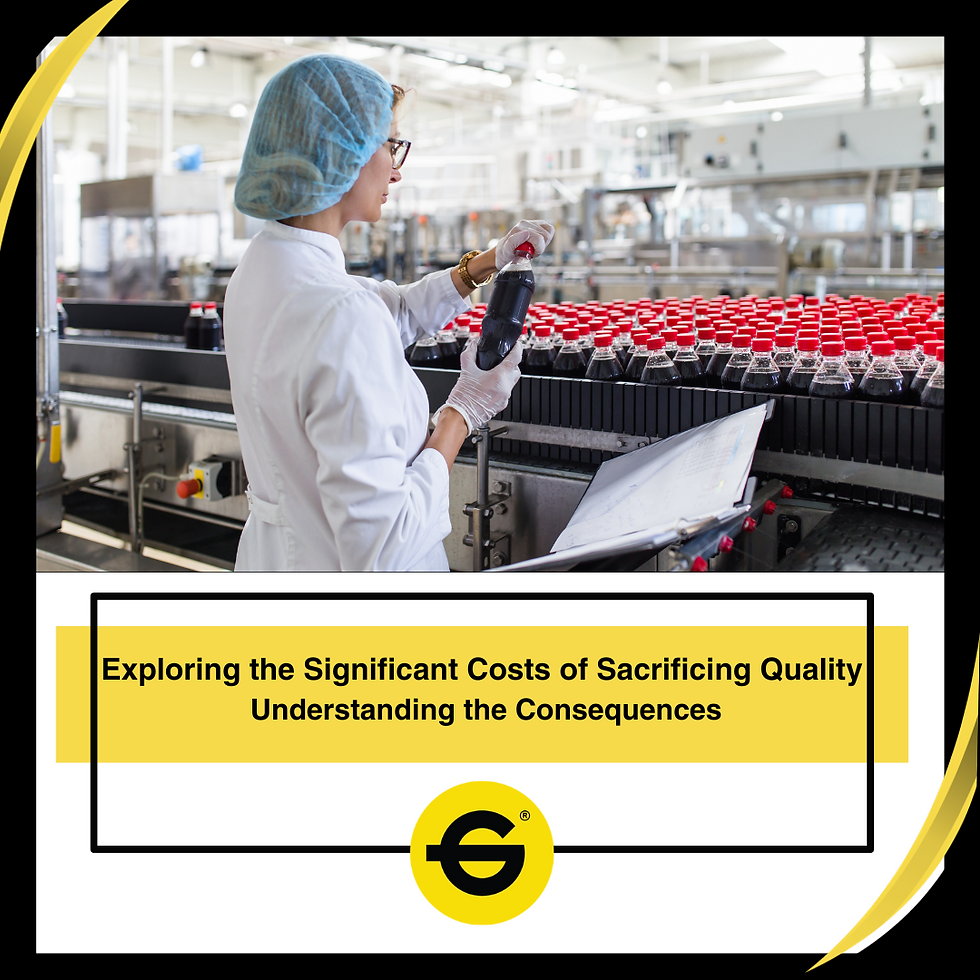
In the contemporary world of manufacturing, the relentless pursuit of efficiency sometimes leads to compromising product quality, a decision that can result in unforeseen and significant financial repercussions. For example, the 2015 airbag errors, one of the automotive industry's largest recalls, impacted about 60 to 70 million units across 19 global manufacturers. This crisis forced Takata, a leading Japanese airbag manufacturer, into bankruptcy by June 2017, with recall costs soaring over $25 billion.
So, how can we reduce defects while scaling up production?
This article will cover:
Exploring Billion-Dollar Recall Cases: Sacrificing Quality for Efficiency
First, let's dissect the Takata case further. The airbag errors not only affected a massive number of vehicles but also tarnished the reputation of multiple automotive giants. Beyond the direct financial costs, the recalls resulted in a loss of trust among consumers. For Takata, the bankruptcy was a devastating consequence of quality lapses. The company had to set aside billions to cover recall-related expenses, which included not only replacement costs but also legal fees, settlements, and regulatory fines. The ripple effect was felt throughout the industry, with other manufacturers also facing financial burdens.
Moreover, the Volkswagen Dieselgate scandal in 2015 stands out as a stark example of compromised product quality. To meet emissions standards, Volkswagen used software that manipulated test results. This unethical practice cost the company roughly $33 billion in penalties, settlements, and vehicle buybacks. Moreover, it severely damaged Volkswagen's reputation and eroded customer trust globally. This case underscores the immense consequences of sacrificing quality and ethical standards for short-term gains.
Another major case was the General Motors ignition switch recall of 2014 is a tragic chapter in automotive history. The recall involved millions of vehicles equipped with defective ignition switches that could inadvertently shut off the engine while driving, disabling critical safety systems like airbags. This catastrophic flaw was linked to at least 124 deaths and incurred a staggering cost of around $4.1 billion, serving as a stark reminder of the dire consequences of compromising product quality and safety in the pursuit of efficiency.
The Ripple Effect on Supply Chains
Additionally, the impact of quality lapses on supply chains is like a stone thrown into a calm pond, creating ripples that reach far and wide. It's not just the company at the epicenter of the issue that suffers; the shockwaves reverberate throughout the entire supply chain. A study conducted by the Journal of Business Research sheds light on the scale of this problem, revealing that 94% of Fortune 1000 companies encountered a disruptive supply chain event in the past year, and many of these disruptions were linked to quality issues. These disturbances create a domino effect, causing delays, escalating costs, and straining relationships with suppliers.
A prime example of this domino effect can be seen in the case of Samsung's notorious Galaxy Note 7 crisis. The exploding batteries not only inflicted a colossal financial loss of $5.3 billion on the company but also sent shockwaves through its network of suppliers and the broader tech ecosystem. Suppliers faced reduced demand for components, resulting in production cutbacks and financial losses of their own. Furthermore, the incident damaged consumer trust in the Samsung brand, impacting sales across multiple product lines. This real-world scenario underscores the profound and far-reaching consequences of compromised quality, extending well beyond the financial realm and affecting the intricate web of relationships within the supply chain.
Defining Quality Control: What Do We Mean By 'Quality' Anyway?
Quality control (QC) is the process through which companies measure, maintain, and enhance the quality of their products or services. At its core, quality control is the compass that guides organizations towards delivering excellence consistently.
According to ISO 9001, the international organization for standardization certification, quality can be defined as "fitness for use," "customer satisfaction," "doing things right the first time," or "zero defects." Webster's dictionary further characterizes quality as "a degree of excellence" and "superiority in kind." Understanding this, we can see why various industries, from automotive manufacturing to healthcare, place an utmost emphasis on implementing stringent quality control measures. Take, for example, the aerospace industry, where the precision and reliability of components are paramount. AS9100 implementation here drives efficiency, cost savings, and consistency while enhancing employee engagement, customer satisfaction, and top management involvement, ultimately resulting in improved financial performance and adherence to stringent quality and safety standards. Quality control in aerospace involves rigorous testing and inspection to ensure that aircraft parts meet exacting standards for safety and performance. Any deviation from these standards could have catastrophic consequences, making quality control an absolute necessity.
Similarly, in healthcare, QC safeguards patient well-being by monitoring the accuracy and effectiveness of medical treatments and procedures, reinforcing trust in healthcare providers. Quality control serves as a common thread that weaves through diverse sectors, underscoring its universal importance in delivering superior products and services.
Significance of Quality Control
Consumer Protection: Quality control (QC) acts as a protective barrier, ensuring that defective or subpar products do not reach consumers. In sectors like technology, food, and pharmaceuticals, where poor quality can have severe consequences, QC safeguards public health.
Commitment to Excellence: QC signifies a company's dedication to excellence. It serves as a promise to customers that the products they receive not only meet but often exceed their expectations. In manufacturing, this commitment results in safer, more reliable products that inspire consumer confidence.
Case Study: Colorado S.A., a leading Moroccan paint producer, achieved ISO 9001 certification in 2003. This quality management certification not only strengthened its commitment to excellence but also led to a 50% reduction in defects. This substantial decrease translated into significant cost savings and heightened customer satisfaction. Colorado's ISO 9001 certification showcases how quality control processes can yield tangible benefits, making it a notable case study in quality management.
Quality Control vs. Quality Assurance: The Two Pillars of Quality Management
While quality control (QC) and quality assurance (QA) might seem interchangeable, they represent different aspects of ensuring product and service excellence.
Quality Control (QC): Managing Product Variability:
Quality Control primarily focuses on the identification and rectification of defects in products or services. It involves the meticulous inspection, testing, and evaluation of individual items or processes to detect any deviations from established quality standards. Think of QC as the 'spot-checker' that examines the end product, ensuring it meets predefined criteria.
In manufacturing, for instance, QC personnel may inspect a random sample of finished goods to verify that they conform to specifications. In software development, it involves rigorous testing to identify and address software bugs. QC is essentially the 'last line of defense' before a product reaches the consumer, preventing flawed items from entering the market.
Quality Assurance (QA): Building Quality into the Process:
On the other hand, Quality Assurance takes a broader perspective. It's not just about finding and fixing defects; it's about preventing them from occurring in the first place. QA involves establishing and maintaining processes and systems that consistently produce high-quality outcomes. In essence, QA is proactive rather than reactive.
QA encompasses a range of activities, from creating robust manufacturing processes to developing comprehensive testing protocols. It ensures that every step of production or service delivery adheres to predefined quality standards. QA doesn't just focus on the final product; it evaluates the entire process, identifying areas where improvements can be made to enhance overall quality.
The Symbiotic Relationship Between QA & QC
While QC and QA may seem distinct, they are intrinsically linked. QC is the 'checks and balances' system that evaluates the final product, while QA is the 'architect' that designs processes to prevent defects. Together, they form a powerful partnership that safeguards quality.
How To Manage Quality Control During Manufacturing Scaling
"What strategies can we implement for quality control?"
Managing quality control while scaling is crucial for businesses aiming to maintain high standards, customer satisfaction, and overall success. According to a Gartner survey, creating a culture of quality can lead to improved customer satisfaction, increased revenue, and reduced costs due to fewer errors and defects.
Implementing Robust Processes: Ford, a major player in the automotive industry, harnessed vehicle data for swift issue identification and resolution, slashing fix times from months to minutes through over-the-air software updates. This approach not only underlines the effectiveness of robust processes in defect reduction and customer responsiveness but also significantly cuts warranty and operational costs.
Setting Clear Quality Metrics: In manufacturing, mirroring Amazon's data-driven approach can be a game-changer. Establishing precise quality metrics, like defect rates or production cycle times, enables swift detection and correction of quality deviations. This proactive approach ensures product consistency, reduces defects, and mitigates costly recalls during scaling.
Leverage Technology: General Electric (GE) employs machine-learning algorithms to predict and prevent defects in its manufacturing processes, saving millions of dollars.
Engaging Suppliers and Customers: Apple's supplier partnership strategy serves as a prime example in the manufacturing realm. Apple invests in its suppliers, offering training and resources to enhance the quality of components used in its products. This collaborative approach has significantly contributed to Apple's manufacturing success, ensuring top-notch quality and customer satisfaction.
Conduct Regular Audits: In the manufacturing sector, Toyota is a standout example of the benefits of regular quality audits. Toyota's famed "Toyota Production System" incorporates frequent audits and inspections at various production stages. This proactive approach has not only helped Toyota maintain high-quality standards but has also fostered a culture of continuous improvement, which is integral to its success in the automotive industry.
Utilize ERP and MRP Systems: Boeing's experience with Enterprise Resource Planning (ERP) exemplifies its impact in manufacturing. Following a production crisis in 1997, where supply chain issues halted assembly, Boeing adopted ERP systems. Despite initial challenges, including a loss of over $1 billion, the implementation streamlined their operations, managing over 1 billion parts annually. This demonstrates the vital role of structured data and supplier involvement in ERP systems for precision and efficiency in aerospace manufacturing.
Redefining The Trajectory and Definition of Quality Control
The evolving landscape of manufacturing quality control extends beyond defect reduction to encompass customer experience, sustainability, and innovation, as recent billion-dollar recalls have underscored the consequences of compromising quality for efficiency. Quality Control (QC) remains crucial, complemented by proactive Quality Assurance (QA) processes. To ensure effective quality control during expansion, manufacturers should rely on robust processes, clear metrics, technology adoption, stakeholder engagement, regular audits, and ERP and MRP systems. The future trajectory of quality control in manufacturing depends on adaptability, innovation, and a commitment to delivering excellence across all business facets.
The article on DevOps incident management process and responding to system failures is insightful and well-written. It provides a comprehensive guide to handling unexpected issues efficiently, emphasizing the importance of communication and collaboration within a team. The strategies suggested are practical and can be easily implemented to improve overall system reliability.
Elevate your online presence with our SEO services. As a Myntra and Flipkart seller, we specialise in optimizing your product visibility on these platforms. With expertise in Amazon sales accounts, we offer a comprehensive solution for digital marketing and e-commerce management. Trust us to expand your brand's performance through strategic SEO, ensuring maximum visibility and attracting potential customers.
https://cruzendigital.com/
Elevate your online presence with our SEO services. As a Myntra and Flipkart seller, we specialise in optimizing your product visibility on these platforms. With expertise in Amazon sales accounts, we offer a comprehensive solution for digital marketing and e-commerce management. Trust us to expand your brand's performance through strategic SEO, ensuring maximum visibility and attracting potential customers.
https://cruzendigital.com/
You may raise your online exposure with Inklick Media's specialized account management services, which are designed for top e-commerce platforms. Work together with us to expand your company's presence and sales on well-known e-commerce platforms such as Amazon, Flipkart, Myntra, Snapdeal, Meesho, Shopclues, eBay, and Etsy. Our experienced team is equipped to manage the subtleties of every platform, ensuring that your products make a significant impact and are seen by a larger number of people. Trust Inklick Media to provide comprehensive solutions that will help your online business reach its full potential.
https://www.inklickmedia.com
In my experience within the logistics and transportation sector, the specter of quality lapses haunts our operations like an ever-looming storm. The repercussions of even a minor slip in quality can send shockwaves through the entire supply chain. Delays, dissatisfied clients, and financial losses become an unfortunate norm. That's precisely why I'm deeply interested in delving into the realm of blockchain technology and its potential to revolutionize our industry. Blockchain's inherent qualities of immutability, transparency, and traceability hold promise for addressing the Achilles' heel of quality control in logistics. If we can embrace and effectively integrate blockchain into our operations, we might just be able to fortify our supply chains against the relentless waves of uncertainty and quality concerns, charting…