What Costs are Associated with Plastic Injection Molding?
- Dustin Craft
- May 23, 2023
- 4 min read
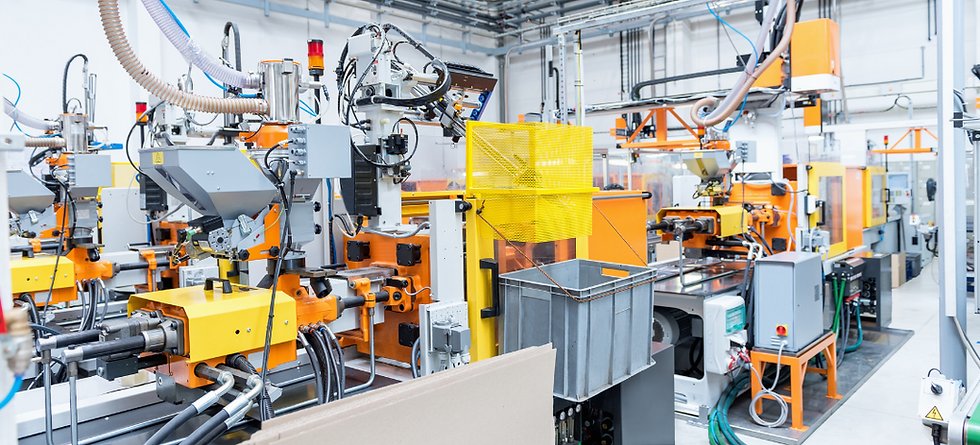
Plastic injection molding is a versatile and widely used manufacturing process for producing high-quality plastic parts and products. It offers numerous benefits such as cost-effectiveness, design flexibility, and high production rates. However, it's essential to understand the costs associated with plastic injection molding to make informed decisions and optimize the manufacturing process.
Below, we've listed the various factors that contribute to the costs of plastic injection molding and provide estimated figures and relevant statistics.
Mold Design and Development Costs
The first major cost associated with plastic injection molding is the design and development of the mold itself. Mold design involves creating a precise blueprint of the part to be produced, considering factors such as material selection, part geometry, tolerances, and production volume. The complexity of the part design and the number of cavities in the mold greatly impact the mold development costs.
The costs of mold design and development can range from a few thousand dollars for simple molds to several hundred thousand dollars for complex molds with multiple cavities. Additionally, modifications or alterations to the mold design during the development process can incur extra costs.
Material Costs
The type and quantity of material used in plastic injection molding significantly influence the overall production costs. The choice of plastic material depends on factors such as part requirements, functionality, durability, and aesthetics. Commonly used plastics include polypropylene (PP), polyethylene (PE), acrylonitrile butadiene styrene (ABS), and polycarbonate (PC).
Material costs can vary depending on factors like the type of plastic, its quality, and the supplier. It is important to consider the desired material properties, such as strength, heat resistance, and chemical resistance, while balancing costs. On average, material costs can account for 20-30% of the total injection molding costs.
Machine and Labor Costs
The injection molding machine is a crucial component in the production process. The machine selection depends on factors such as part complexity, size, and required production volume. High-quality machines with advanced features may have a higher initial investment cost but can yield improved efficiency and reliability.
Labor costs associated with plastic injection molding include the wages of machine operators, quality control personnel, and maintenance staff. Skilled labor is essential to ensure proper machine operation, part inspection, and maintenance. Labor costs can vary depending on geographic location, labor market conditions, and skill level required. It is estimated that machine and labor costs together contribute to approximately 20-35% of the total production costs.
Overhead Expenses
Overhead expenses are indirect costs associated with plastic injection molding and are incurred throughout the production process. These expenses include utilities, facility maintenance, insurance, administrative costs, and general overhead. Overhead costs are usually calculated as a percentage of the direct production costs.
Typically, overhead expenses account for around 10-15% of the total injection molding costs. However, this can vary depending on the size of the manufacturing facility, location, and specific business overheads.
Secondary Operations and Finishing
In some cases, additional operations and finishing processes may be required after the plastic parts are molded. These secondary operations can include trimming excess material, drilling holes, adding inserts, applying surface finishes, or assembling components.
The costs of secondary operations depend on the complexity and quantity of additional steps required. It is important to consider these costs when evaluating the overall production budget.
Tooling and Maintenance Costs
Tooling costs refer to the expenses associated with maintaining and repairing molds throughout their lifespan. As molds are subjected to wear and tear during the production process, regular maintenance is essential to ensure consistent part quality and prolong the mold's lifespan.
Tooling costs typically account for a small portion of the overall injection molding costs, ranging from 2-5% of the total production costs. However, neglecting proper tool maintenance can lead to increased downtime, decreased productivity, and the need for more frequent mold replacements, significantly impacting the overall costs.
To mitigate tooling costs, it is crucial to implement a proactive maintenance schedule, regularly inspect molds, and address any issues promptly. Additionally, working with a reputable mold maintenance and repair service provider can help optimize tooling costs and extend the life of the molds.
Quality Control and Testing
Ensuring the quality and integrity of the molded parts is vital in plastic injection molding. Quality control processes such as dimensional inspections, material testing, and functional testing are necessary to meet industry standards and customer expectations. Quality control expenses include equipment costs, testing materials, and skilled personnel required to perform inspections and tests.
While quality control costs can vary based on the complexity of the parts and the level of testing required, they typically account for 3-5% of the overall production costs. Investing in quality control measures upfront can prevent costly rework, scrap, or customer returns in the long run.
Shipping and Logistics
Once the plastic parts are manufactured, they need to be shipped to the desired destination. Shipping and logistics costs depend on various factors, including the part's size, weight, packaging requirements, shipping distance, and transportation method. International shipments may involve additional customs fees and import duties, further impacting the overall costs.
To optimize shipping costs, it is advisable to work closely with reputable logistics providers who specialize in handling plastic injection molded parts. They can offer cost-effective shipping solutions while ensuring timely and secure delivery.
Optimizing Plastic Injection Molding Costs
While plastic injection molding entails several costs, there are strategies to optimize the process and minimize expenses:
Design Optimization: Collaborate with experienced designers and engineers to optimize part designs for manufacturability, reducing material waste and improving production efficiency.
Tooling Considerations: Invest in high-quality molds that can withstand the production demands and require minimal maintenance. Regularly maintain and repair molds to prevent unplanned downtime and additional expenses.
Material Selection: Choose the most suitable plastic material for your specific application, considering cost, performance, and availability.
Production Volume: Analyze the required production volume and evaluate whether it is more cost-effective to produce parts in-house or outsource to a specialized injection molding company.
Process Efficiency: Continuously improve production processes, reduce cycle times, and minimize scrap rates through automation, advanced machinery, and skilled labor.
Supplier Evaluation: Conduct thorough research and choose reliable material suppliers, mold makers, and other partners to ensure consistent quality and competitive pricing.
Conclusion
Plastic injection molding is a widely used manufacturing process that offers numerous benefits, but it is essential to understand the costs associated with it. Mold design and development, material costs, machine and labor expenses, overheads, secondary operations, tooling and maintenance, quality control, and shipping expenses all contribute to the overall costs. By optimizing design, material selection, production processes, and partnering with reliable suppliers, manufacturers can minimize costs and maximize the benefits of plastic injection molding. Understanding the various cost factors enables informed decision-making, ensuring successful and cost-effective plastic injection molding operations.
Comentários